Matthew Freed Pottery
Art for everyday life
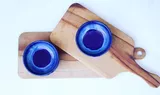
Matthew Freed Pottery
Art for everyday life
The Process
Pottery is complicated. It is an art that requires creativity and a strong sense of design. It is also a science that requires a thorough understanding of natural materials and how they will react in combination with extreme heat. Each piece is a complexity of nature, science, and art. It amazes me.
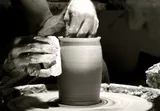
Think it
The process begins with an idea. The idea can be initiated by the end function of the piece, by the aesthetic form and design or often by a combination of these stimulants. Inspiration can strike in strange ways.
In the past, ideas have been sparked by analyzing the overhead lights on an airplane, fossils in granite steps, and a three-legged dog.
Form it
Before beginning to throw a pot on the wheel, clay is wedged (kneaded like dough) to remove any air pockets and to get the molecules in the clay moving. Once the clay is centered on the wheel, it is ready to be formed. The piece is formed by combining clay, water, and careful manipulation of hands, fingers, and some funny looking tools made of wood, plastic or metal.
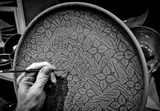
Finish it
The finishing stage fine-tunes the form and design of the piece. Finishing takes place after a formed piece has dried out until it is "leather hard". (It can be handled without damage, but can still be worked in certain ways).
At this stage, bottoms of pots can be trimmed, a pot can be paddled or bent into a different shape, the pieces of a teapot can be put together, handles can be put on pitchers, and decorative patterns can be carved in the clay.
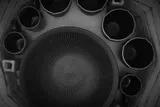
Fire it
When a finished piece has dried further, it is ready to be bisque fired. Until clay comes into contact with heat, it cannot be termed pottery. Bisque firing strengthens the pot considerably and allows the potter to handle the pot more readily without fear of breakage.
Bisque firings are best done slowly so that the remaining water turns to steam and escapes slowly so as not to force off sections from the wall of the pottery. When a piece is bisqued, it is then ready to be glazed.
I mix all my glazes from scratch and have worked hard to developed my own unique palette of colours and textures. Once the glaze is applied, the piece goes back into the kiln for its final firing.